Asset History and Activity Use Case
Asset / Vehicle Utilization and Location History
Automated measurement of asset utilization, trip reporting, time on site, runtime, location history and idle time.
Overview
Measure and analyze asset utilization across your whole fleet and by asset. Gain awareness and visibility of:
Vehicle Trips
Start time, end time, trip distance, trip duration.
Driver Behavior
Speeding, harsh braking or cornering.
Location History
Where assets have been, how long they have been on site, what they have been doing.
Time On Site
How long have assets been at a location, have they been running, provide evidence for billing.
Runtime and Mileage
Keep track of maintenance milestones automatically and transform planned maintenance from reactive to proactive.
Idle, Condition and Time In State
Understand idle time, how long assets have been running without working or forgotten and underutilized. Understand how long assets are in downtime and in need in repair (time to fault resolution).
The Problem
Vehicle and asset centric business operate fleets of mixed equipment types that are essential for productivity and generating revenue. Most of these businesses can find it difficult to track their inventory and whereabouts, let alone understand how their assets are being used and by whom. They often lack visibility of their fleet and have a range of utilization questions:
- Where are my assets?
- What are they doing?
- How long have they been working?
- Are they sitting idle?
- Which jobs or sites are they being used at?
- What maintenance requirements are coming up?
- How to I provide proof of service and billing evidence to my clients?
- How do I know what my field staff are telling me is correct about work time and utilization?
- Is my equipment being hoarded?
- Do I really need all these assets? Can we downsize or do we need to reallocate assets?
- Do I need to hire a replacement or additional asset, or do I have an available asset in my inventory?
- Where is all my inventory? Is it lost, stolen, forgotten, misplaced?
- Inconsistent compliance as operators forget or ignore pre-start requirements or they figure no one really looks at the inspections anyway.
- Human error leads to mis-identification of assets or data entry errors leads to the wrong assets being updated with the wrong information. This creates compounding problems where the wrong asset is serviced, wasting parts and time, while the asset that actually required service or repair is still in need of service. Once these data entry issues occur it undermines your wider asset management and maintenance programs.
- Equipment is out of compliance or issues are unattended and neglected as inspections are not completed consistently or are lost or damaged. Even when inspections are entered into systems such as spreadsheets, jobs have restrictive visibility due to limited access to information.
Pain Points
Lack insight into asset location and utilization.
Asset are lost or misplaced, can’t keep track of inventory.
Don’t know who is using assets, where or for how long.
Don’t understand how vehicles are being used, where they have been, time on location or who is using them.
Customers question billing and it is difficult to resolve disputes without evidence of asset use and time on site (lack proof of service).
Questions about asset productivity and idle time leave management frustrated and create trust issues and friction with staff.
Vehicle and asset maintenance is reactive, lacks forward insight and leads to unplanned downtime, delays and additional costs.
Fleets are not right-sized. No insight into over or underutilization. No insight into where assets are needed most.
Unnecessary equipment hire as suitable assets cannot be located or there is limited insight into equipment availability. This leads to avoidable additional costs.
The Solution
Blackhawk provides a comprehensive solution for smart, digital forms. These forms can be easily customized and updated in real-time and instantly available to field user via mobile browser, iOS or Android application. This includes:
The Benefits
Digital inspections and checklists provide a range of benefits:
Who Benefits
Operational Teams
Improve operational efficiency and visibility of assets, workflow automations and digital convenience. Digital forms make operator’s and driver’s lives easier.
Maintenance / Service
Improve resource planning and visibility of maintenance needs as well as real-time alerting and supporting information such as location, timestamps and photos.
Management
Asset managers and C-level management have greater oversight and insight of asset maintenance and lifecycle. Compliance is better managed, and safety and compliance standards are measured and visible.
Finance
Greater maintenance efficiency leads to lower costs, improved productivity and utilization, leading to improved profitability.
Use Cases
Here are some real-world examples of how we apply digital inspections and checklists for asset management:
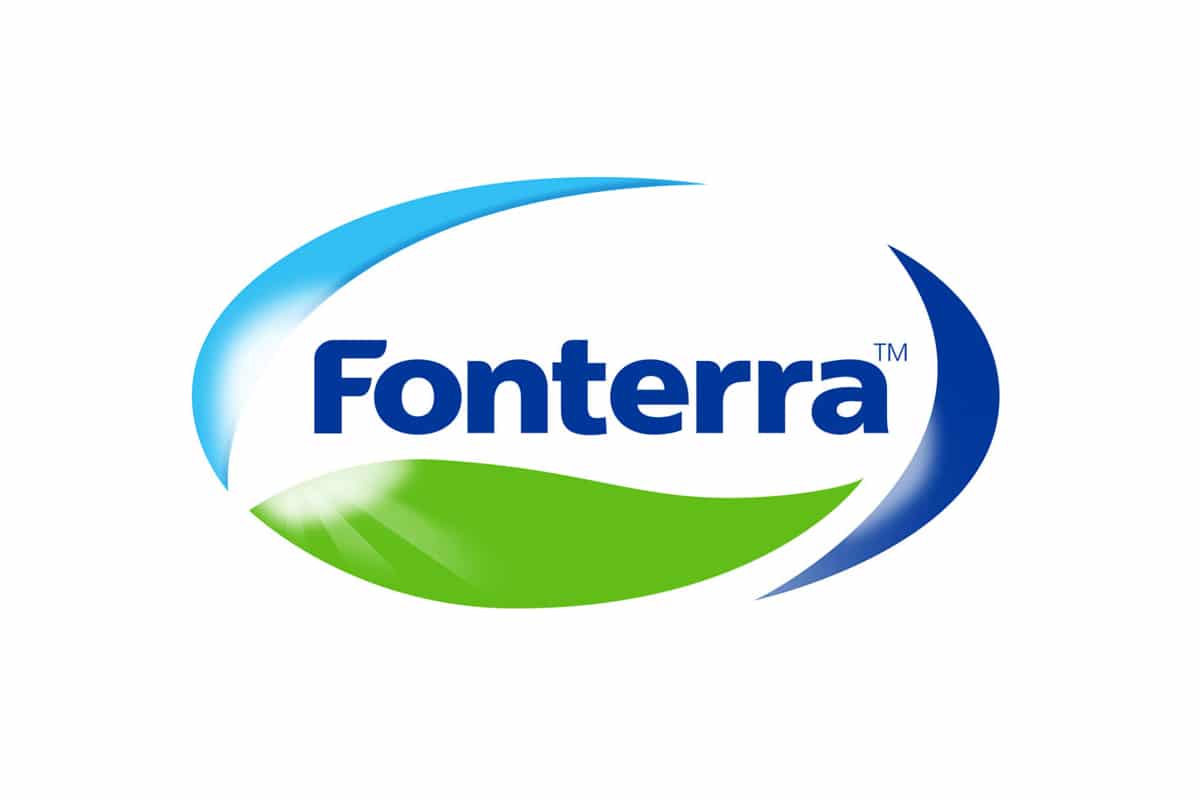
Contract Forklift Maintenance (AB/Fonterra) (NZ)
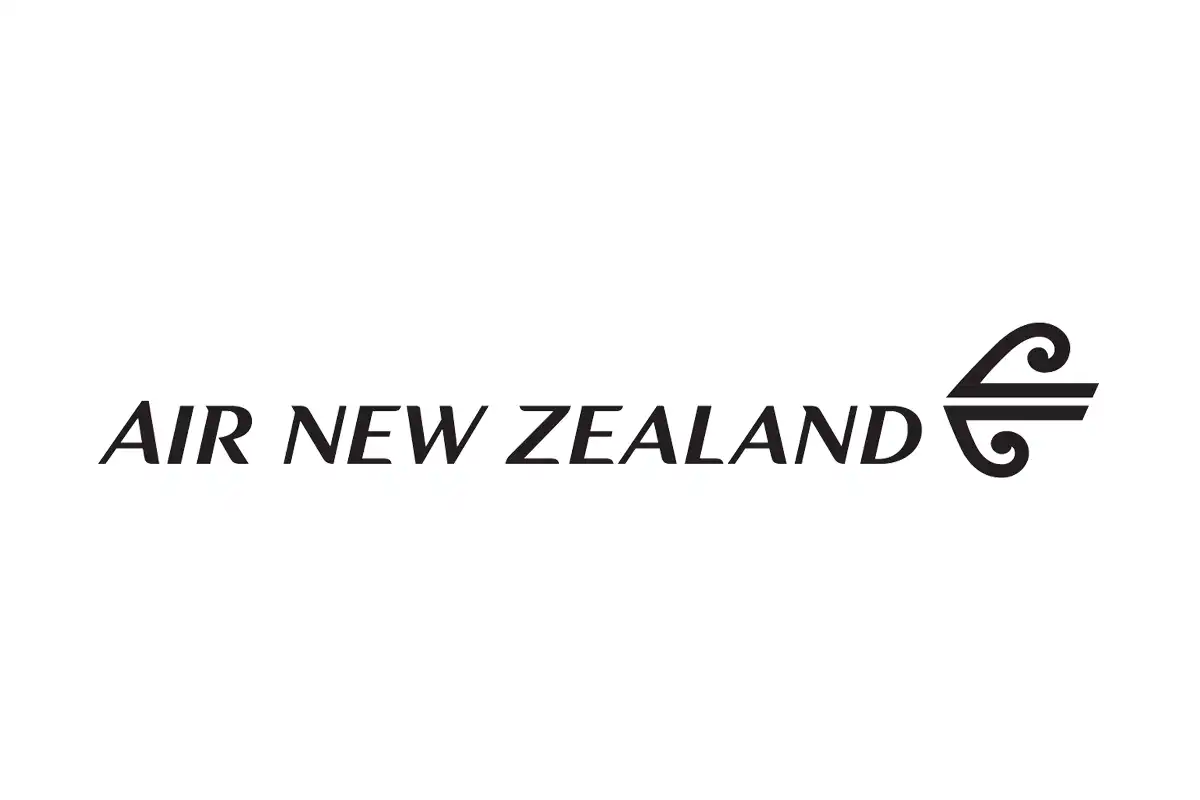
Contract GSE Maintenance (AB/AirNZ), Wheelchair Tracking
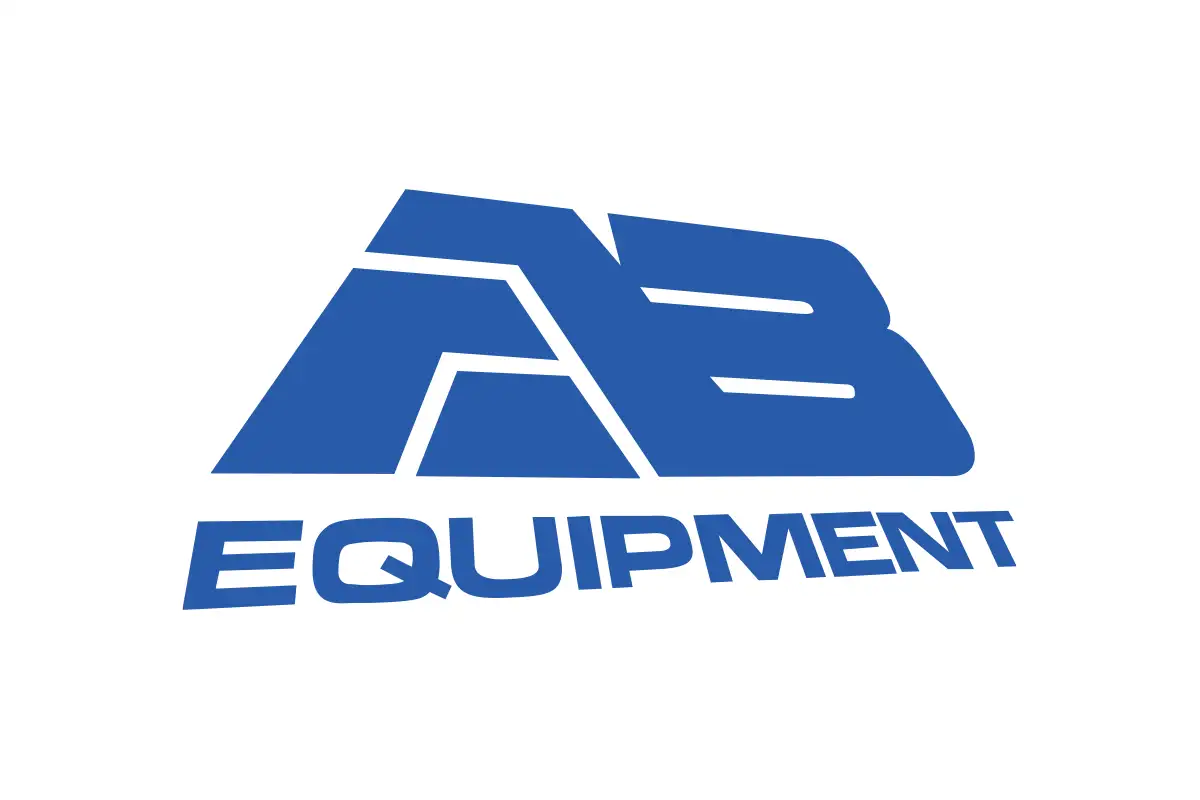
Forklift & GSE Maintenance (AB)
Thinxtra / GSE Airline Operations
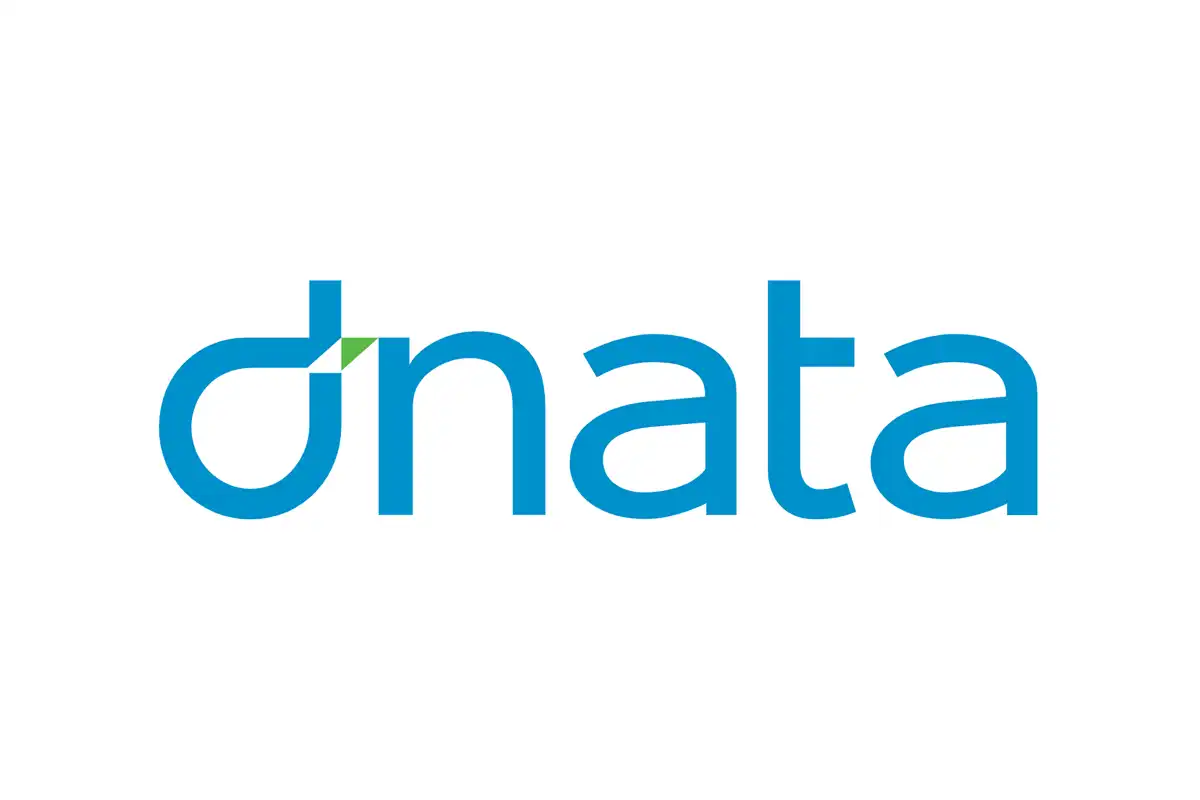
Wheelchair Tracking (AU)
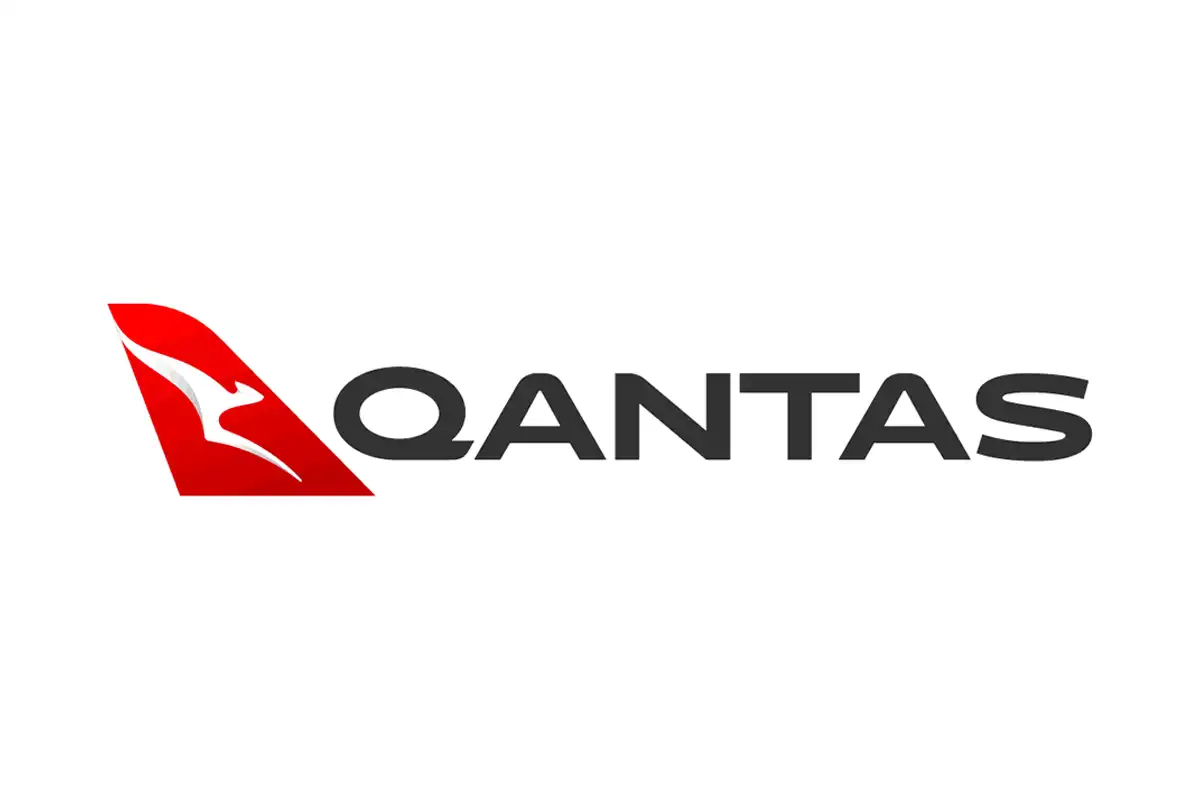
Wheelchair Tracking (AU)
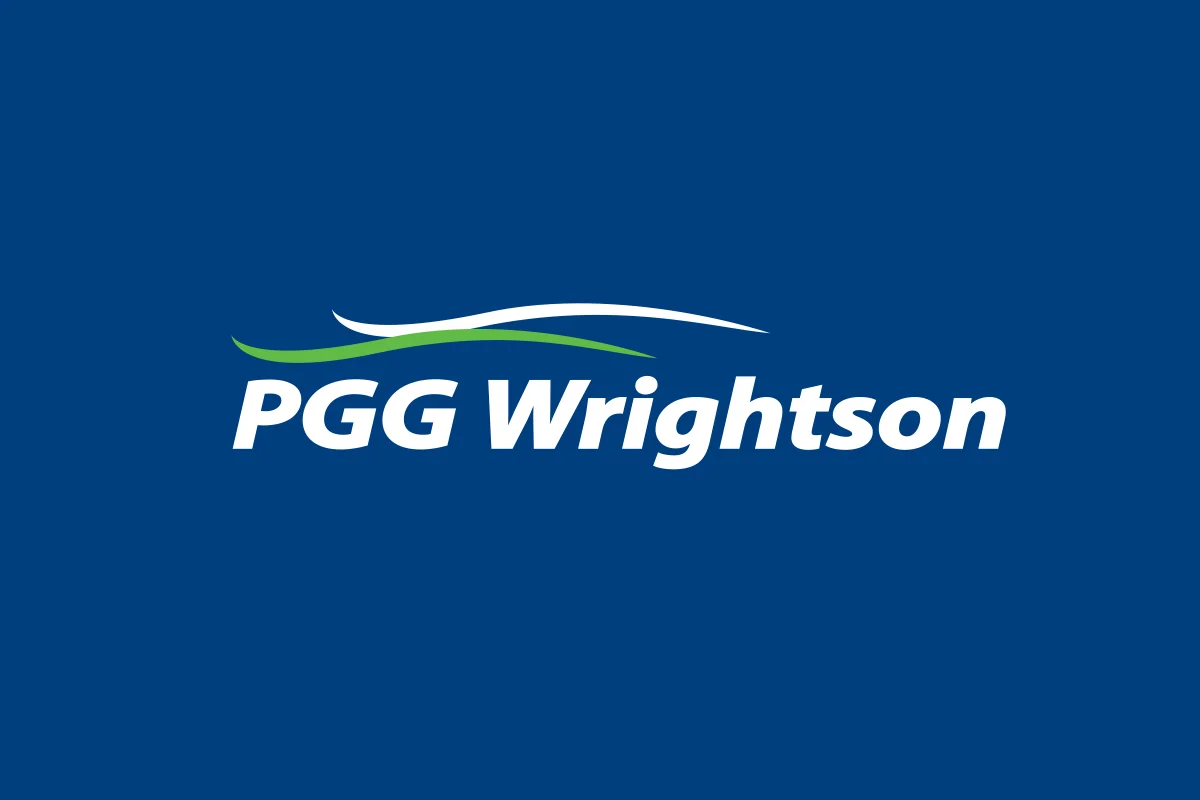